SiO2: Properties and Applications
The Universal Compound
Silicon dioxide (silica) is one of the most commonly encountered substances in both daily life and in electronics manufacturing. Crystalline silicon dioxide (in several forms: quartz, cristobalite, tridymite) is an important constituent of a great many minerals and gemstones, both in pure form and mixed with related oxides. Beach sand is mostly silica. The working of silica into glass (usually by the addition of natron -- sodium oxide -- to lower the melting point) has been known since antiquity, with polished glass lenses in eyeglasses and optical instruments dating back more than 5 centuries. The whole of planar electronics processing and the modern IC industry has been made possible by the unique properties of silicon dioxide. It is the only native oxide of a common semiconductor which is stable in water and at elevated temperatures, an excellent electrical insulator, a mask to common diffusing species, and capable of forming a nearly perfect electrical interface with its substrate. Deposited silicon dioxide, almost always by CVD approaches, is almost as old as thermal growth on the substrate, and has been employed in various ways in IC fabrication due to its familiarity, versatility, and reliability.
Let us examine this interesting material. SiO2 is formed by strong, directional covalent bonds, and has a well-defined local structure: four oxygen atoms are arrayed at the corners of a tetrahedron around a central silicon atom: (click link for an animated version)
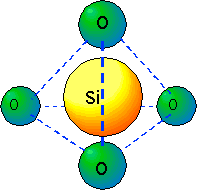
The oxygen atoms are electronegative, and some of the silicon valence electron density is transferred to the oxygen neighbors, but it is incorrect to regard the material as a salt of a Si[+4] ion with O[-2] ions, as is sometimes seen in the literature: the directionality of the bonds is essential to the observed structures.
The bond angles around O-Si-O are essentially the tetrahedral angle, 109 degrees; the Si-O distance is 1.61 Å (0.16 nm) with very little variation. The bond distance is slightly smaller than the sum of the conventional covalent "radii" of the atoms: Si (0.11 nm) + O(0.066 nm) = 0.18 nm. Thus we ought to show the atoms as slightly penetrating each other; the sphere size was shrunk in the diagram above for clarity.
It is the oxygen "bridge" bonds between silicon atoms that give SiO2 many of its unique properties. The bond angle Si-O-Si is nominally about 145 degrees, but can vary from about 100 to 170 degrees with very little change in bond energy. Furthermore, rotation of the bond about the axis is almost completely free.
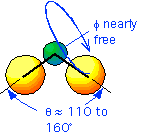
A convenient way of summarizing these observations (known as the Zachariesen-Warren model for the structure of SiO2) is that the "tetrahedra" formed by the SiO4 groups must touch each other at their corners, but can do so at widely varying angles: (again click the link for a spiffy animated version)
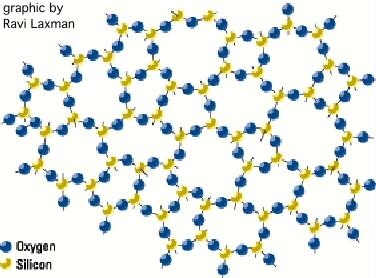
The result of this flexibility in the bridge bonds is that SiO2, while it has many different possible crystalline structures, can very easily form amorphous materials (i.e. materials with no long-range order). Essentially all deposited and thermally grown oxides in semiconductor processing are amorphous. Unlike e.g. amorphous silicon, amorphous silicon dioxide will not crystallize upon annealing at normal temperatures. ("Devitrification" -- that is, crystallization -- of quartz furnace tubes used for high-temperature oxidation is sometimes observed after thousands of hours of use at temperatures exceeding 1200 °C.) The amorphous structure is tends to be very "open": even in thermally-grown oxides, channels exist through which small positive ions such as Na+ and K+ can readily migrate. These ions can move under the influence of electric fields within the gate oxides of MOS transistors, causing shifts in the voltage at which the transistor turns on ("threshold shifts"). Exclusion of such ions is imperative for reliable operation of MOS transistors and integrated circuits.
Let's look at some important properties of pure SiO2:
density 2.0-2.3 gm/cm3 electrical conductivity varies widely breakdown field >1E7 V/cm in thermal oxides; can be as low as 1E6 V/cm in CVd oxides thermal conductivity 0.01 W/cm K (bulk) thermal diffusivity 0.009 cm2/sec (bulk) coefficient of thermal expansion 0.5 ppm/ K [note Si thermal exp 2.3 ppm/K] refractive index 1.46 [thermal oxide] dielectric constant 3.9 [thermal oxide]; CVD oxides vary widely depending on H
It is important to note that many of the properties of SiO2 show wide variability, because of the flexibility of the structure mentioned above. Chemically pure silica has been prepared in at least 35 crystalline forms with density varying by more than a factor of 2 (17 to 43 SiO2 units per 1000 cubic Angstroms). Chemical properties such as hygroscopicity (tendency to react with ambient water) vary tremendously depending on the structure. [reference: "Structural Similarities and Dissimilarities between SiO2 and H2O" F. Liebau in The Physics and Technology of Amorphous SiO2, ed. R. A. Devine, Plenum (NY) 1992]
I've seen a lot of work using the refractive index at optical frequencies to characterize silica. I'm not sure why, unless the joke about looking under the lamp post (the light is better) applies: n doesn't vary much and can vary for many reasons. Dielectric constant at DC-to-microwave frequencies, and infrared absorption are much better ways to characterize SiO2.
Chemistry
Interaction with hydrogen and water are important in semiconductor applications of silicon dioxide. Hydrides such as silane (SiH4) and DCS (SiH2Cl2) are often used as precursors for silicon dioxide deposition, and water is ubiquitous in the ambient. Some important reactions are:

The first reaction has little change in enthalpy and is nearly reversible; locally strained bonds, with reduced bond energy, are particularly vulnerable to attack by water (hydrolysis). Oxides containing large amounts of SiOH are more hygroscopic, and readily adsorb water molecules from the air. The water can migrate through the deposited materials to the gate oxide, there causing drifts in performance of transistors under bias, impairing hot electron reliability, also known as gate oxide integrity or GOI. The water molecules can, however, be consumed by the reactions with Si-H groups: this is the basis of the use of silicon-rich oxides as water getters or barriers.
Deposited oxides often have strained bonds and reduced density. At temperatures of around 650 to 700 °C, local structural readjustments become possible; oxides annealed at temperatures above 700 °C for a few minutes are normally found to be densified, with reduced hydrogen content and improved stability in subsequent anneals or exposure to ambient moisture. However, very high temperatures indeed are necessary to completely remove moisture and erase all memory of the deposited structure. Isolated Si-OH will survive anneals at over 1000 °C, presumably because there's nowhere for the hydrogen to go: it needs to find another hydrogen to be removed as H2 or even H2O. As the concentration of H at the surface is reduced this becomes increasingly improbable. Adding hydrogen atoms from e.g. a hydrogen plasma helps desorb the remaining isolated SiOH. [reference: "Thermal Stability of Hydroxyl Groups on a Well-Defined Silica Surface", O. Sneh and S. George, J Phys Chem vol 99, p. 4639 (1995)]
Applications
Intermetal dielectric:
- "etched-aluminum" metallization: the "IMD" layer must fill high-aspect-ratio gaps between metal lines, provide good electrical insulation, have low stress to avoid cracking or cause reliability problems for aluminum metal, and have low moisture content to avoid gate hot electron reliability problems. High deposition rates are needed to keep cost down.
- Damascene metallization (copper): here the metal lines are "inlaid" into trenches etched in the silicon dioxide layer. Thus the SiO2 is always deposited onto a planar surface; the stringent requirements for topography coverage that apply to etched-metallization are not relevant. The other requirements (low moisture content, controlled stress, high rate) are still important.
Isolation:
- Shallow trench isolation: Shallow trenches are etched in the silicon substrate through the active layer to isolate neighboring transistors. Here silicon dioxide is used as a trench fill material; low stress is important to avoid defects at corners of trench
- LOCOS: This is the older method of isolating transistors: a thin sandwich of silicon nitride and silicon dioxide is deposited in the locations where transistors will later go to prevent oxidation there, and elsewhere a thick field oxide is grown. CVD SiO2 is used in sandwiches with deposited silicon nitride for patterning and selective oxidation.
DRAM capacitors:
- SiO2 was used in a sandwich with nitride for the poly capacitor dielectric. In these applications, it has mostly been replaced by high-K dielectrics.
Doped Oxides: PSG and BPSG
In IC processing it is often important that each deposited layer end up with a flat surface upon which to build and pattern subsequent layers -- planarization. One means of planarizing a layer is to melt it and let it flow as a liquid, minimizing surface tension and thus curvature. It is highly desirable to use such "flow" processes with dielectric layers to smooth out the rough edges of underlying features such as polysilicon gates. However, pure silicon dioxide requires temperatures of 1300-1400 °C to flow readily; this is much too hot for other features on the wafer to tolerate. Introduction of "dopants" (really more like alloying elements, as they are used in percentage quantities) can reduce the melting point of the glass. Traditionally (as noted above) sodium oxides have been used to soften glass, but sodium ions are unacceptable for electronic applications. Thus, addition of phosphorus or boron (PSG, BSG, and BPSG) is used. (Arsenic is also occasionally employed as a dopant.)
Phosphosilicate glass (PSG) flows readily at 1000 °C for 6-8 weight% P in the alloy. An additional benefit of adding phosphorus is the gettering of small positive ions: Na is trapped at trivalent P atoms and thus prevented from migrating. PSG was thus a very popular first deposited dielectric layer after transistors are formed (also known as a contact dielectric or ILD). However, PSG has important limitations. The flow temperature cannot be made lower by adding more phosphorus, because the additional material becomes susceptible to interaction with ambient moisture to form phosphoric acid. In trace quantities, the acid leads to corrosion of subsequent metal layers and poor reliability; in large quantities gross extraction in air occurs, leading to degraded flow properties and lithography defects. Phosphosilicate glass is also used as a final passivation, typically in a sandwich with silicon nitride, because of its gettering properties for positive ion contamination.
Borophosphosilicate glass (BPSG) can achieve a lower flow temperature: typically around 900 °C for 4-5 wt.% of each dopant. (Note that 4 weight % of boron is a very large mole percentage -- around 12 at.% depending on composition-- because B atoms are so light.) BPSG was the contact dielectric of choice in many early CMOS processes.
Like PSG, the amount of dopants that can be added while remaining stable on exposure to the atmosphere is limited. For high B concentrations, crystals of boric acid form at the surface of the oxide on exposure to air; high P films give phosphoric acid. Stability in air is usually poorest after deposition and improved after flow, so it is not uncommon to require that flow processes be performed within a few hours of deposition -- a significant inconvenience in a production facility. Further, high dopant concentrations can lead to the formation of crystals of boron phosphate (BPO4) within the oxide during anneals, particularly during the cooldown step. BPO4 is actually a thermodynamically stable phase when B and P concentrations are high, and causes defects since the crystals are not readily etched in wet HF or fluorine plasmas. The practical limit for minimum flow temperature appears to be about 850 °C for post-flow or 800 °C for films deposited at high temperatures (i.e. flow in situ). These temperatures are too high for advanced logic devices, so flowed BPSG was generally replaced by CMP-planarized films.
Summary of Precursors and Deposition Methods
Precursors Technique Applications SiH4, O2; PH3 and B2H6 as dopants; 400-500 C Showerhead APCVD ("Pyrox" reactor) obsolete Tube LPCVD BPSG Injector APCVD BPSG, PSG final passivation TEOS, O2; TMP and TMB as dopants Tube LPCVD ("HTO"); 700 C spacer oxides, gate oxide sandwich, isolation sandwich; BPSG PECVD; 300 - 350 C intermetal dielectric (dep/sputter etch or sandwich with TEOS/O3); cap layers for BPSG or PSG; final passivation SiH4, N2O PECVD, 200-450 C cap layers and barrier layers for spin-on glass; final passivation TEOS, O3; TMP and TMB as dopants Showerhead "SACVD", 200-700 Torr, 350-500 C, or injector APCVD, 350-500 C IMD sandwich; BPSG; final passivation; spacer oxide
Return to Tutorial Table of Contents
Book version of the CVD Tutorial